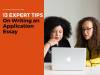
Water Distillation
Out of all the water purifier innovations utilized in the drinking water industry, water distillation or refining is the main procedure that duplicates the hydrological cycle: water is boiled until it starts to steam; the steam is cooled to condensate, making water, expelling the impurities abandoned in the boiling process. It is a straightforward evaporation-condensation-precipitation process.
The most widely recognized solo strategy for expelling contaminants from feed/source water in the bottled water industry is RO, with about 40% of U.S. bottlers utilizing this method, contrasted with an expected 15% that use distillation method. The remaining 45% of bottlers either don't get rid of contaminants since they produce and market mineral or spring water.
Cost is one of the principal reasons why not many bottlers use distillation. The significant cost factor is equipment.
The expense of energy required to heat the water to boiling in the distillation procedure has made even the expense of creating a gallon of distilled water much more costly than RO. In any case, new distillation innovation has addressed that challenge.
Over the long haul, distillation can be very economic. While RO ordinarily makes 1 gal of wastewater for each gallon of bottled water produced, distillation produces up to 6 gals of product water for each gallon of wastewater. Top-quality water can be created by distillation from basically any source: streams, lakes, wells, springs, and municipal supplies. Due to the continuous boiling procedure, any microbiological contaminants are killed.
Learn more about the types of Water Distillation System
- Vapor Compression
Vapor Compression is the method of water distillation process by which a compressor, jet ejector, or a blower is utilized to compress and then increase the pressure of the vapor produced. Since the pressure increment of the vapor likewise creates an expansion in the condensation temperature, a similar vapor can fill in as the heating mechanism for its "mother" solution or liquid being concentrated, from which the vapor was produced in the first place. On the off chance that no compression was provided, the vapor would be at a similar temperature as the boiling solution/liquid, and no heat transfer would take place.
Additionally, in some cases, it is also called Vapor compression distillation (VCD). If the compression is performed by a precisely driven blower or compressor, this evaporation procedure is typically referred to as Mechanical Vapor Recompression (MVR). Likewise, the process is called steam compression or thermocompression in cases of the operation conducted by high pressured motive steam ejectors.
- Multiple Effect
Multiple Effect distillers are less complex in structure. With no moving parts, there is practically nothing that would wear out. Distillers with more than one evaporator are intended to reuse the heat energy which made the steam in the first boiler to warm the water in the second boiler. A dual-boiler unit creates double the distilled water as a single boiler unit for a similar cost. A four-boiler unit generates four times the water, and a six-boiler unit will deliver 6 gallons of water for the rough expense of distilling 1 gallon of water.
Multiple Effects gets its name from the utilization of more than one boiler to create distilled water. Multiple Effect systems use about two to six boiling effects/chambers. If there are more chambers then the water distillation is produced more efficiently.