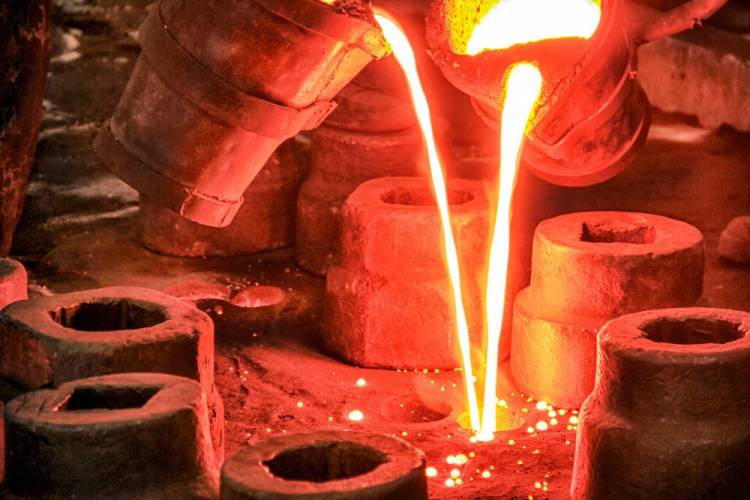
Investment Casting And Its Task
Lost Wax Casting
Investment casting, every so often known as a lost wax casting, is a metal outlining strategy known for its ability to make leaves behind close protections, complex inside openings, and exact estimations. Investment casting produces accurate parts while restricting material waste, energy, and coming about machining. It can in like manner ensure the production of complex parts. This makes the endeavor casting measure truly significant to design engineers.
Components, for instance, plan necessities, cost, and reasonableness to create direct which casting measure is for the most part fitting to make a thing. This article depicting investment casting is wanted to help you make an informed casting decision.
Task:
Investment casting manufacture is a sort of casting measure by which significantly complex parts can be quickly made. There are chief strides to the hypothesis casting measures, The underlying advance incorporates making the wax plan that will eventually be the last condition of the parts. Wax is utilized because it is easily relaxed and reused, nonetheless, this moreover infers that a wax model should be used once each time a segment is made. This imperative requires the maker to have a sort of master shape, which can be reused to make the wax plans.
These can be exorbitant because they ought to be tweaked to each part, and are unstable to perfect if especially low protections are required. In any case, if any of these molds are made, they can be related through a wax bar which considers one pour to project various parts. Finally, a dirt pouring cup is added to the most noteworthy mark of the wax plan, so producers will have a channel to exhaust the fluid metal into the last shape.
The second step in the investment casting measure is where this finished-up wax configuration, complete with runners and sprues, is dunked into a clay difficult slurry. This liquid generally contains inconceivably fine silica, water, and various latches. Exactly when plunged, the part will be peddled in a petite layer of slurry, which is satisfactorily a state of the wax plan. This plunging step is done numerous events over to achieve a particular coat thickness, and thereafter, the part is dried. In the wake of drying, the part is flipped around and warmed to both kill wealth sogginess and mollify away the wax inside. As of now, makers are left with a vacant stoneware type of their optimal part.
Fluid Metal
The third step will happen soon after the second, where creators will purge fluid metal into the fine art when it is at this point hot from the drying measure. This pre-warming from the past advance holds the fluid metal back from hurting the ceramic shape, similarly as works on the movement of the metal into fine corners/detail locales. Similarly, as the social occasion chills off, both the terminated shape and the metal will contract, giving better dimensional exactness to the main wax plan. After the metal is casting, makers hold on for it to cool completely.
The fourth and last development to theory casting is to part away from the artistic expression when it is absolutely solid. This is routinely gotten done with water jets or various methodologies for wiping out the artistic layer without hurting the key metal. Presently, the finished parts are fit to be cut from their runners and cleaned to their optimal end-product finish.
It's anything but's a model with comparable nuances as the finished part, of course, really there is a payment for warm pressure. Models are regularly made of wax using a metal imbuement to fail horrendously. At the point when a wax configuration is made, it is assembled with other wax sections to outline the entrance and runner metal transport system. Dependent upon the size and plan of the best consummation fragment, diverse wax models may be ready to use a single tree.
The entire wax configuration get-together is plunged in an earth slurry, covered with sand mortar, and allowed to dry. Examples of wet plunging and coming about stuccoing are repeated until a shell of the best thickness is made. That thickness is mostly coordinated outcome size and game plan. At the point when the shotshell has dried, it ends up being sufficiently strong to hold the fluid metal during casting.
At the point when the casting has cooled enough, the framing shell is parted away from the casting in a knockout movement. The entryways and runners are cut from the casting, and if crucial, the last post-taking care of sandblasting, crushing, and machining is performed to finish the casting dimensionally. Non-ruinous testing may join fluorescent penetrant, alluring atom, radiographic, or enhance examinations. Last dimensional evaluations, composite test results, and not are affirmed before shipment.